
Solutions
Operational excellence focuses on optimizing business processes, increasing speed, decreasing waste and eliminating non-value-added time. Cadence has considerable experience deploying Lean Six Sigma tools to streamline business processes, build internal capability and improve profitability. Our team has experience working with industry leaders such as GE, Raytheon, Texas Instruments and Honeywell. Our consultants will help you define customized solutions from strategy development through deployment. We help you achieve:
Cost
Decrease Cycle
Time
​
Product development through delivery to the customer
​Decrease production costs by 30-50% across the value stream
Quality
Build quality into processes and products
Inventory
Decrease total inventory & implement control measures

Perfection is not attainable. But if we chase perfection, we can catch excellence.
Vince Lombardi

Average results of lean transformation in companies in differing industries and sizes: Productivity increase 25%
Manufacturing Advisory Service in the UK

LEAN
We utilize a systems approach to implement lean manufacturing based on the Toyota Production System, recognized for maximizing productivity and eliminating waste.

SIX SIGMA
Our team has expertise in implementing and training Six Sigma theory and tools, helping you identify and eliminate the causes of variation and increase predictability.
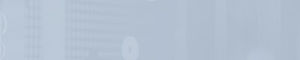
PROBLEM SOLVING
Our team will help you utilize the best problem-solving tool for the situation, assisting with gap closure. This may include: Toyota’s 8-Step Problem Solving, A-3, Plan-Do-Check-Act, and Six Sigma DMAIC approach.
CHOOSE THE RIGHT TOOLS
•
Whether it is a targeted task area, supporting the value stream, or a functional process that needs significant improvement—we can help.
SERVICES
FACTS

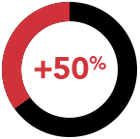
Best-in-class operations companies generated 50% higher sales growth than their industry peers
Cohen & Roussel, Strategic SCM: The Five
Core Disciplines for Top Performance, McGraw-Hill Education, 2013
Average results of lean transformation in companies in differing industries and sizes:
On-time delivery increase 26%
Manufacturing Advisory Service in the UK

Enterprise-Wide Continuous Improvement Programs
Considering adopting a Lean Six Sigma program to ignite performance excellence and gain cost savings? We can help you develop a strategy and plan for an enterprise-wide Continuous Improvement program and provide guidance through every step of implementation.
​
Mentoring and Coaching Leadership
With a breadth of operational experience, we work closely with leaders to guide the improvement process. Working as an extension of your internal team, we partner with your organization to provide guidance and transfer knowledge
​Continuous Improvement Training and Development Programs
We provide training in: Lean Six Sigma, Continuous Improvement Leadership Deployment, Change Management and in specific problem-solving methodologies. Our goal is to quickly transfer information and knowledge so that your team takes ownership of continuous improvement, waste and cost-reduction processes.
Continuous Improvement Projects
Whether it is a targeted task area, supporting the value stream, or a functional process that needs significant improvement—we can help. Our subject matter experts will coach your team or lead a Continuous Improvement Project. We provide a wide range of support:
Lean project implementation
Kaizen and Value Stream Mapping facilitation
Project management for site and business-wide implementation
Strategy development and deployment
•
•
•
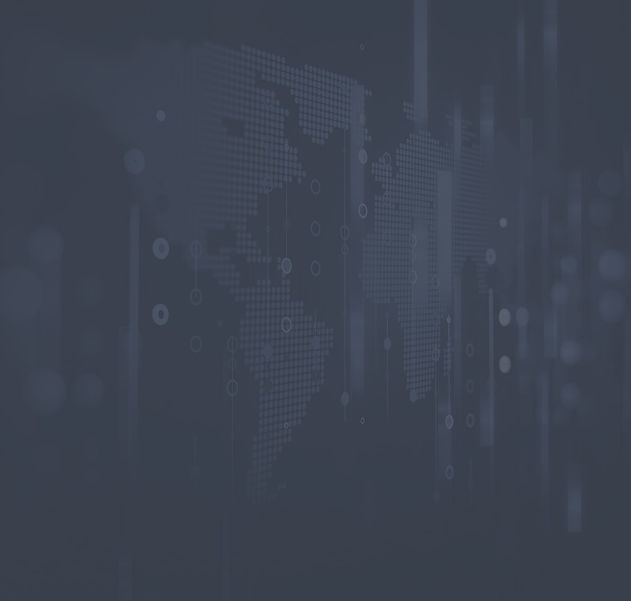
PROCESS
Define: Clearly identify the problem
​
Measure: Use metrics to understand impact on results and performance
​
Analyze: Determine root cause through observation and measurement
​
Improve: Use continuous improvement tools to eliminate process waste and improve performance
​
Control: Implement controls and counter-measures to sustain performance
•
DMAIC approach to problem solving

•
•
•
•